Wasp Barcode Technologies: The Barcode Solution People
Top 7 Roadblocks Inventory Managers Face
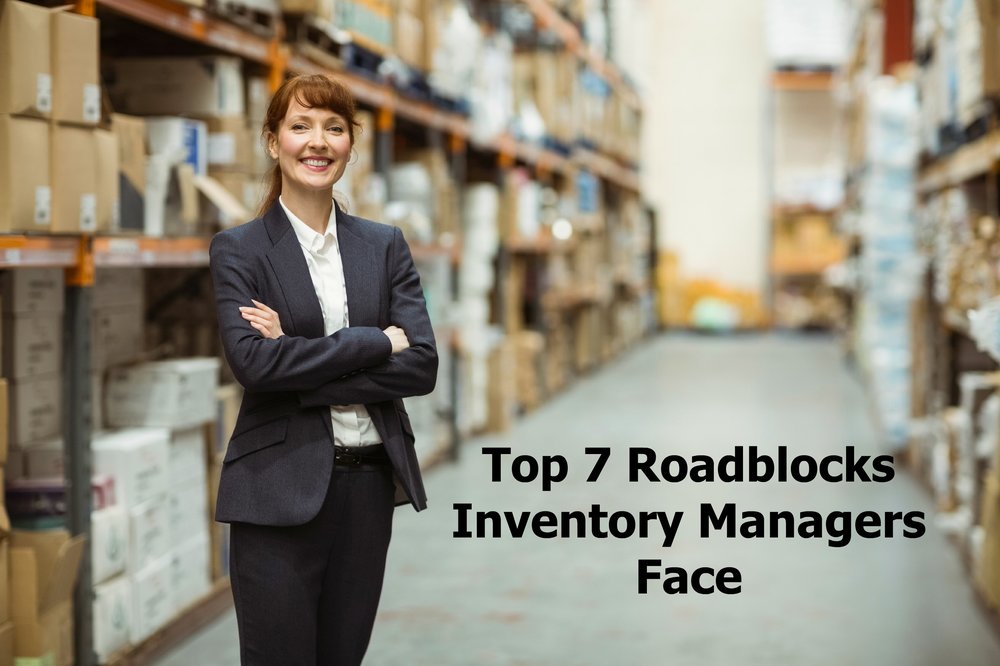
Inventory managers have an overall goal to ensure that their warehouse operations are flowing efficiently with individual items in and out of existing inventory. More specifically, you want to control all the inventory so your unit numbers don’t become too high or conversely too low to the point that your company’s business will come to a complete halt.
Great inventory management is a balancing act, consisting of a number of tasks across operations. Just as important as these tasks is overcoming challenges that simply come with the job.
1. Efficiency
Inventory managers walk a fine line of warehouse efficiency every day. If just one operational process is out of whack, that can trickle down into every other department. For example, if your warehouse employees have to manually key in SKU numbers into your system, there’s a much higher risk of human error. If an item has the wrong SKU, then customers could end up ordering the wrong item….and receiving a package they didn’t expect or want. If this happens frequently, then don’t expect to have very satisfied customers.
That’s just one example from one honest mistake. Simple human error can mean big losses for your business over time if this sort of thing becomes the norm.
[su_divider top="no" size="2"]
[su_divider top="no" size="2"]
2. Don’t Just Think About Automation, Do It
According to Boston Consulting Group
research, 1.2 million robotic systems are being utilized at companies worldwide. Depending on your type or size of business, robots may be a bit much. That doesn’t mean automation is out of reach. You can start with deploying an inventory management system. It can be integrated into your processes easily, affordably, and with little to no downtime.
[Tweet "1.2 million Robotic systems are being utilized at companies worldwide."]
- Optimize labor productivity
Productivity should be the cornerstone of your warehouse and a key part of building efficiencies. Disorganized physical space or lengthy, hard-to-understand processes can stand in your way. There are many practical ways and inventory manager can
combat productivity challenges and help you understand your productivity rates. Here are a few to get you started:
This determines the entire flow of the warehouse. Your picking begins at one end of the warehouse and ends at the wrapping staging area.
- Organize a bin by top hits
If it is properly binned, most of your picks will be done in the first 20 percent. Reevaluate the top hits items regularly. Inventory is a living breathing animal that always changes.
- Incorporate manifests: Two examples include:
- Picking manifests allow a number of orders to be pulled at once. If you have a large order, it can be picked separately, and several smaller orders can be combined into one picking manifest where they are separated in final boxing.
- Loading manifests Always allow for some “wiggle room” in your loading manifests. There will always be that one company that needs an order by a certain time. In general, each route should come out in suggested delivery order. It comes out in reverse order, because the first thing you load is the last thing you deliver.
- Maximize Vertical Space Maximize every inch of space in the warehouse from floor to ceiling. Pallet racking is one of the most popular storage used in most manufacturing facilities, warehouse operations, and even in many retail stores. It opens up space, improves overall efficiency, and makes for a safer working environment, according to a Health & Safety article.
3. Accuracy
Do these statements sound familiar?
“Because of our distribution center problems, we have to audit 100 percent of orders after pickers complete them.”
“The inventory accuracy at our last physical inventory has significantly dropped in the past five years.”
“We still have so many inventory errors, even cycle counting can’t fix them.”

If you manage inventory at one of the
46 percent of companies that use manual inventory processes, not only does efficiency lag, but accuracy is basically nonexistent. As an inventory manager, it’s up to you to really know what inventory you have on hand, if excess or obsolete items are building up, or if high demand is causing a shortage.
Any of those scenarios cause revenue losses, create warehouse space issues, accrue high inventory costs, and decrease customer satisfaction. Again, the implementation of an
inventory management system can solve those problems by eliminating human error and touch points because the real-time data it can provide helps you make better business decisions.
4. Redundant Processes
Any process that has to be repeated
wastes time, Even something as simple as a worker illegibly writing down a SKU number could result in another worker trying to figure out what the SKU number is for an item and re-entering it. Simple human error can really add up over time. Redundant processes also negatively impacts employee productivity.
If you know this is happening within your warehouse, it’s time to reevaluate your current operations and streamline workflows, eliminating any redundant or even unnecessary procedures. Then your productivity rates will improve, efficiencies will be optimized, and accuracy will increase.
5. Warehouse Layout
Maybe you hear
rumblings like this around your warehouse:
“We are totally out of space and about to increase our off-site space.”
“Our warehouse space is not being used efficiently.”
“Our warehouse layout is not keeping up with our evolving business.”
If so, then there are things you can address to fix the problems with your warehouse:
- Flow: Be sure your warehouse is arranged in a logical sequence of operations, with each activity is as close as it can be to what precedes it and follows it. Controlled and uninterrupted movement of materials, people and traffic is key, with the goal of no cross flow clashes, back-ups, or disruptions.
- Accessibility: This not only means getting to the products you need, but can you also get to the required level of pack? Bottled water and pharmaceuticals are a good example of this. For water, you might have to access down to the case level in a warehouse or down to individual bottles in a convenience store stock room. For pharmaceuticals, accessibility is often needed down to a specific lot or batch number.
- Space: When you plan out your warehouse space, the available space maximum should be used for allocation of operational storage and stock processing. The minimum space should be used for associated functions such as extra work areas, back offices, and storage. There is a wide variety of storage media available today, allowing inventory managers to optimize every bit of vertical space along with floor space. The best thing is that these changes can be made without a lot expense or disruptive changes to the actual building.
6. Throughput
When you think about efficient throughput, important aspects to consider have to do with velocity of products through the flow of the warehouse. These include handling characteristics, such as:
- Dimensions
- Hazard
- Bulk
- Fragility
- Security requirements
- Compatibility with other products.
The velocity of the product will directly impact how many products move through your warehouse each day. The availability
of real-time access to accurate throughput data greatly assists inventory managers to know the outcome of a design or layout of the warehouse.
7. Making Employees Feel Valued
It can be easy to get wrapped up in processes. Make sure you
care just as much about your employees as you do your processes and customers. A simple thing would be to put down fatigue mats on concrete floors where employees have to stand for long periods of time. Research even shows that music increases productivity. Another tip is to control the climate as much as you can with space heaters or fans. Even if you run a controlled climate warehouse, extreme cold or heat from the outside can drastically affect your workers. Lastly, consider
employee feedback. Make them feel like their opinion matters; After all, they are in the trenches of the business every day.
When you show that you do care about their comfort and opinions, your all-around business will be better.
How have you overcome challenges in your warehouse?